Sheathing
So the good news is, we’ve passed our latest inspection (building inspector comes out at specific points in the construction and gives the go-ahead to proceed). The trusses were braced (there’s a catwalk down the centre so we can get up in there if necessary).
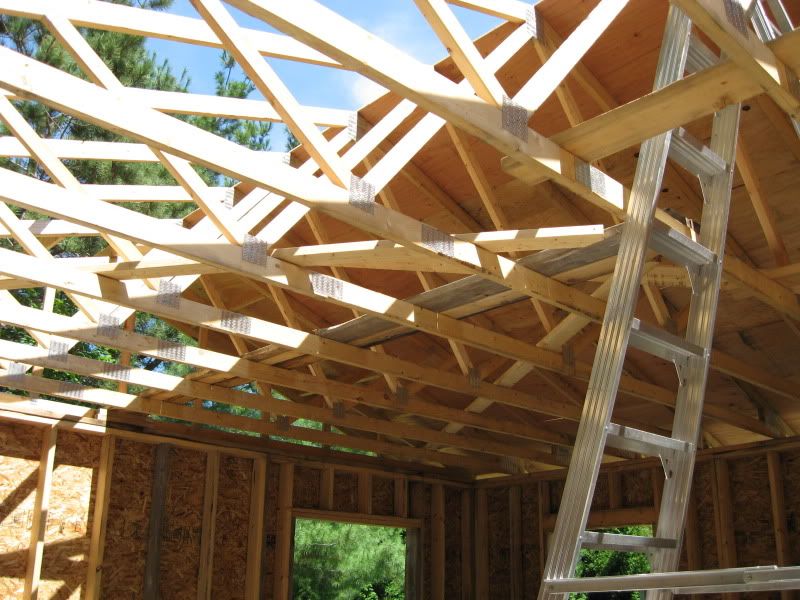
Youngest son has stuck around to help with the sheathing, luckily, as it was obviously too much for the Mr. and me on our own.
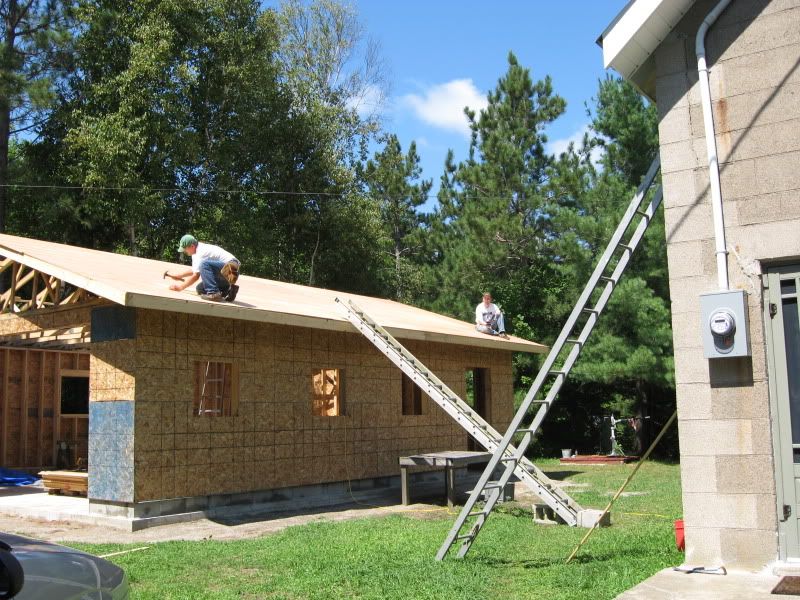
Took a couple of days to do the plywood (with a day off for torrential rains). Since we don’t have a forklift to lift the entire skid of plywood to roof height (I wish!) we slid them one at a time up a gently sloped ladder. Being short I used a length of strapping to help push it to the top (me on one side of the ladder and younger son on the other). The Mr. grabbed each sheet from the edge of the roof and hauled it on top of himself like a blanket then edged backwards until he could stand and drag it to wherever it was needed. Those would have made some great photos, eh? But if there had been an extra person to man the camera we would have shanghaied them into helping out!
The metal roofing is a piece of cake comparatively. It’s longer, but lighter, and is stood on its end at the edge of the roof and then dragged into place.
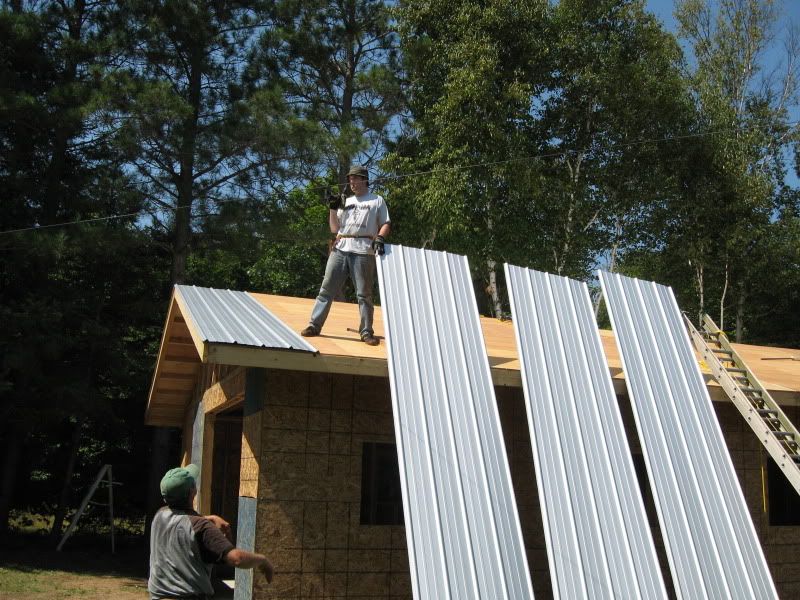
The biggest downside of the metal roofing is the glare of the sun – ouch! – and how hot it gets. They had to take a break at 2 pm to escape the glare and heat.
Not being needed for the metal roofing I’ve been keeping busy with the mature (dry) brush piles building kindling “corrals” – a sort of Lincoln log structure of large branches filled with smaller kindling to be used in the wood stoves. We have at least one brush pile for each of the last six summers so there is a fair bit of tidying up to be done. Keeps me out of trouble.
No more than got the roof ridge and the chimney flashing installed than it started to rain.
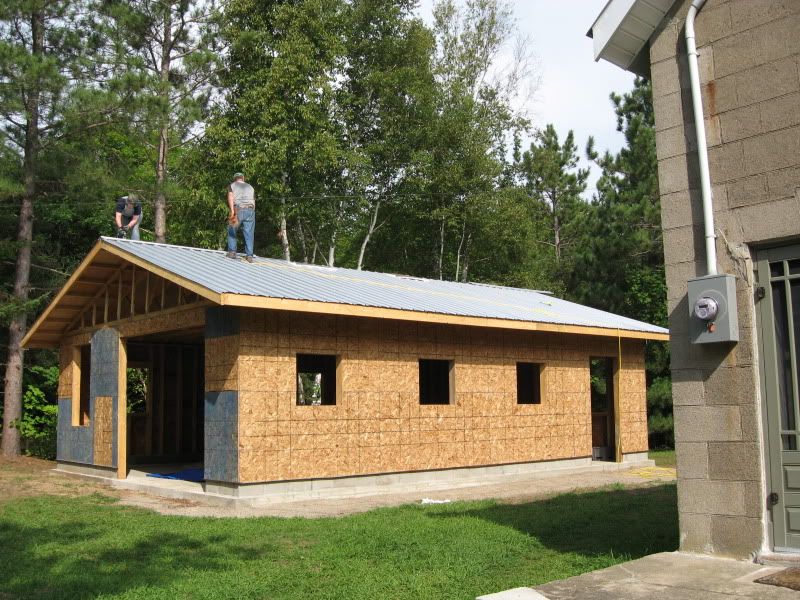
Finishing up loose ends. Fill the gable ends with OSB and cut out gable vent holes. Stuff the ends of the roof ridge with metal window screen so the bats can’t get in. I didn’t get a photo of the rather nifty foam gaskets for under the roof panels (at the top and near the fascia end) to deter insects from nesting in the ridges. Housewrap (Typar) until we run out.
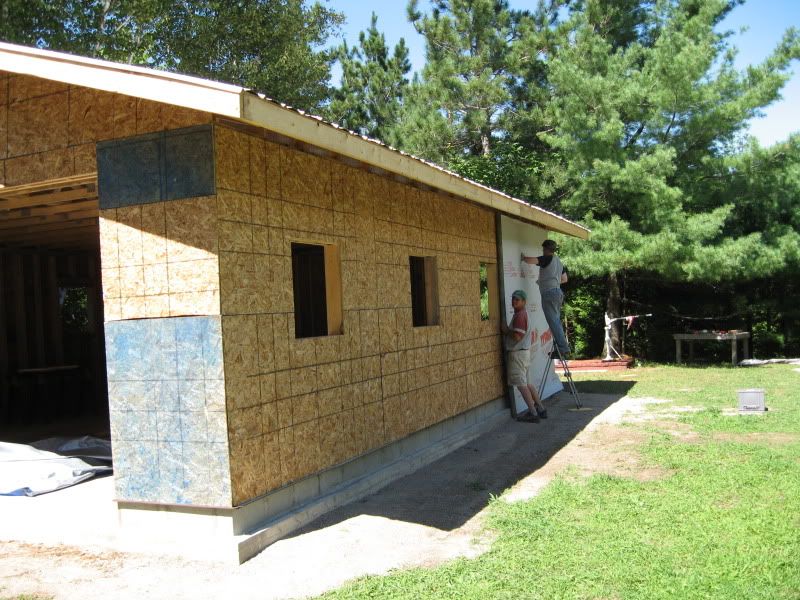
osso, I realize I may not have totally answered your question about the colours on the OSB. The side that goes towards the inside (or down if you use it for roofing) has writing on it, telling me it’s made by Georgia Pacific, which mill, strength direction, blah, blah, blah. The outside has a grid pattern in grey to help keep nailing patterns straight I guess, and to help with setting it up level.
Bits and pieces. Finish off the typar – the place looks like a crazy quilt. Son dug a trench to run electric from schoolhouse to garage (in conduit for extra durability). There’ll be a sub-panel in the garage and we’ll get a licensed electrician to do the hook ups. Son also went back under the floor to run the cable. Let’s hear it for younger son! (Seriously, I don’t know how we would have managed the roof, housewrap and under the floor work without his help.)
The Mr. will probably start the wiring next as the siding isn’t ready. He will need my help with the siding but from here on out he can do a lot of the work on his own.